To inform on imminent crimes, actual or reasonably suspected economic, financial or goodwill damage to the interests and assets of the Group of Companies.
Learn morePress: MODERN, HIGH-TECH, INNOVATIVE: the Principles of Work of the Leaders of the Oilfield Service Industry November 08, 2023
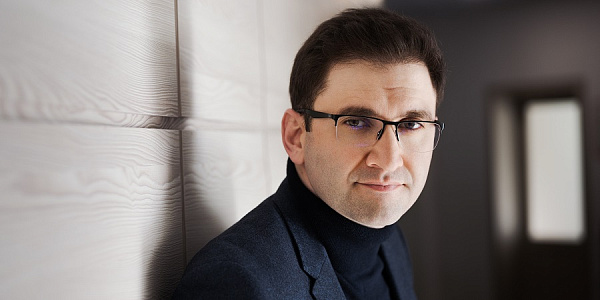
The Russian oil and gas industry is facing new challenges. Finding solutions to unforeseen problems is becoming a daily routine. What helps Russian oilfield service companies not only to maintain their positions in the market, but to keep on developing without deviating from their plans? This and other questions of Neftegaz.RU magazine are answered by Islam Nazaraliev, General Director of NaftaGaz .
– Islam Zamirovich, we met at the beginning of the year, and NaftaGaz as usual had many plans, and the company declared 2023 the year of efficiency. What are the preliminary results?
“Every year the challenges become more and more serious and we have to solve problems at the moment, constantly improving our competencies in recruitment, in developing our own technologies, in expanding the pool of partners. But so far, we are effectively coping with all the challenges.
Recently, the drilling segment of NaftaGaz has onboarded five more crews. In general, we’ve had a rotation of production personnel. Today, we have increased requirements to the quality of the specialists we employ, but for this we offer a completely different level of conditions and social benefits. At the same time, we, like all oilfield service companies, still suffer from a shortage of personnel in all areas and at all levels. The problem of personnel in the oil and gas industry remains very acute.
Production indicators continue to grow: by 21% compared to 9 months of the previous year. We have reached a stable 100,000 meters penetration rate per month and resumed cooperation with the Zapolyarye project, where the flagship of our drilling fleet – drilling rig БУ-6000, produced by Uralmash Oil and Gas Holding, is currently operating. We are working at the Severo-Komsomolskoye field under a contract with a new partner, SevKomNeftegaz LLC.
Our service division ”Naftagaz-Service” and IT enterprise “Digital Drilling” provide services not only for Naftagaz-Drilling, but also for other companies in the market.
Naftagaz-Developement is the first training center in Noyabrsk established for training and advanced training not only of our personnel, but also of oil and gas companies as a whole. Recently, we have purchased modern training complexes and are expanding the curriculum. This year, the center moved to a new comfortable building with modern classrooms, an assembly hall, a canteen, an augmented reality simulator allowing to simulate drilling process, VR systems for practicing industrial safety standards, and much more.
– Oilfield service enterprises have faced the problem of replacing foreign equipment and materials. Now that a year and a half has passed since the introduction of stiff restrictions, has anything changed since then, or was import substitution not a problem for your company?
“We adhere to the principle that the decisions made should be modern, technologically advanced and innovative. Back in 2019, we gradually began to switch to Russian-made software products or create our own. Therefore, the crisis in the IT industry of the last year did not affect us, we did not depend on foreign software. In addition, we are engaged in the creation of our own production solutions for the use of high-tech methods in drilling. There are no more than three such solutions in oilfield services, and one of them is ours.
Today NaftaGaz is the only oilfield service company in Russia that has all drilling rigs equipped with automation systems that ensure minimization of the human factor, improvement of industrial safety and economic efficiency. Moreover, we already offer this service to the market.
– What kind of innovations are being introduced in the field of digital drilling?
"The automated drilling system (ADS) created by our development engineers optimizes the well construction process and improves performance by reducing costs and drilling time. It includes a single digital platform, automatic speed maintenance, a module for surface oscillation of the drill string, a module for reducing the unevenness of rotation/damping, an automatic system for feeding the bit and maintaining the specified parameters of the drilling mode, a system for selecting an optimal drilling mode according to MSE algorithms, a module for preventing downhole incidents, and a module for assessing the work of drillers. Among the results achieved at NaftaGaz facilities after more than a million meters have been penetrated is the increase of mechanical rate of penetration by 25%. The effect for the customer is a 7% reduction in the time of well construction.
– Has the project been implemented or is it under development? What is the overall strategy for implementing the digital project?
- Of course, it is under development. Technological systems, as we know, become obsolete even when they are implemented. Today, we are working on a high-quality visualization of ADS (automated drilling systems) and data analytics to increase the usability. And the most important task is to develop a solution for drilling using a “single button” approach not only for drilling with rotation, but also in a “slide” mode, that is, all operations from the beginning to the end of the build-up. In addition, we plan to replicate a solution for complex oscillation (both for downhole equipment and surface module) to achieve an increase in the length of the horizontal wellbore without the use of a rotary steerable system (RSS). In order to reduce the non-productive time and increase economic indicators, we will introduce a unique offer – a full-fledged integrated monitoring system for drilling equipment to increase the service life of drilling equipment, monitor its condition and ensure timely maintenance and repair, and take preventive measures.
The effectiveness of a digital project still largely depends on people, the quality of their professional training and interaction with each other. In the near future, in order to improve the professionalism, it is planned to introduce a talent pool system and a program to further motivate employees, improve the skills of field engineers and direction managers, and train drilling foremen in the use of a digital drilling rig as a tool for performing geology and geophysics surveys according to the set targets.
– We have been following the activities of your company, and in recent days there has been a piece of news in all industry news feeds about a record at the Yem-Yegovskoye field, where Naftagaz specialists have significantly shortened the drilling cycle. What is the reason for this, because each new record should not depend on the use of a new technology?
– The record at Yem-Yegovskoye field was made using the well-known Fish bone technology, but the joint work of the team, engineers and customer representatives showed an excellent result - the work was completed 11.5 days ahead of schedule. There are records in daily penetration, in drilling speed, in mechanical penetration rate using an automatic drilling complex, the longest horizontal well has been drilled, our team has built a well that has become a record in terms of initial flow rate for our customer - over 1000 tons per day. The drillers of NaftaGaz are not just great, they are the best!
Of course, a lot depends on qualifications, technology and equipment, but teamwork still has a significant impact. And it's not just about the drilling crew, as it's usually a well-coordinated team, it's about communications between the customer and the contractor. In today's realities in the oil and gas industry, these relations have moved to a different level: interaction is going on in all areas including working conditions, technology, and personnel training. An ecosystem with a common knowledge and competence base is being created in the industry.
– The company's plans for 2023 included ambitious plans for investment projects and the development of new business areas. Did you manage to implement them?
– Yes. We continue to implement the strategy for equipment revamp and digitalization. I have already mentioned the latter above. As for the equipment, in the near future we plan to reach 5 years as the average age of the drilling rig. In recent years, we have allocated about 11 billion rubles for the renewal of fixed assets, which were spent, among other things, on 12 new drilling rigs with a lifting capacity of 225, 320 and 400 tons.
At the final stage, the implementation of the project for the development of a universal БУ-250 drilling rig with a great ease of assembly is underway in order to reduce the time of well construction (derrick installation and drilling) by 20% and increase the performance during rig assembly work by two times and during well drilling (reduction in the duration of non-drilling operations) by 5%.
In order to improve the economic efficiency and quality of work, an automated complex for the inspection and repair of drilling tools has just been commissioned. Thanks to new CNC pipe cutting machines, as well as an expanded range of pipe repair works, including, in particular, hardbanding and extreme pressure treatment using phosphating, we will be able to significantly increase the service life of drill pipes. The complex fully covers our needs, and we are ready to provide services to other enterprises.
– In the last interview, we noted that at the end of 2022, NaftaGaz was recognized as the best drilling contractor of Gazpromneft PJSC. This year, you were recognized as the “best employer in drilling”...
“Both awards are very important for us and demonstrate that the company knows how to maintain a balance between business efficiency and human-centricity. Indeed, today we are reaching a new level of interaction with the team. The company's priority is increased attention to living conditions: we introduce modern rotational residential complexes with all the elements familiar to a person in everyday life, provide free meals to shift workers, as well as other services that ensure comfort and allow people to fully concentrate on work.
We are developing the automation of processes, both in the field of production and personnel management. The employees of the company must have such qualifications that allow them to complete production tasks in specialized programs, even if the employees are in the field.
The remoteness of most of the staff from each other led to the development of a corporate portal (using the method of corporate services), which allows you to solve all your questions and tasks using a mobile application, to be in a single information field, and to communicate. Even without internet access, the employees can send HSE documents for reporting, for example. Our oilfield service company was the first to implement such functionality on a large scale. We are systematically moving towards the digitalization and automation of the driller's workplace.
We place considerable emphasis on communication, feedback, and the expansion of the social benefits package. It is worth noting that wages are constantly indexed and all employees will be provided with a VHI (voluntary health insurance) policy from the beginning of next year. In general, we pay special attention to health issues. For a year now, the corporate program “Health: Personalized Medicine for Everyone” has been in effect, which allows the employees to control the risk of cardiovascular diseases and introduce a preventive component into the usual lifestyle of employees. NaftaGaz joined the regional program “Reproductive Health in the Yamalo-Nenets Autonomous Okrug”. Participation in the program is free of charge for the employees, all costs are borne by the company.
Today, NaftaGaz has gathered a very effective team of managers and production workers who perfectly understand the goal we are moving towards. Therefore, we prioritize the principles of maintaining the loyalty of the personnel and personnel development, building long-term relationships between the company and the employees. A drilling crew is a team within a team, and the less is the staff rotation, the more well-coordinated is the teamwork, the more effective are the results. This is typical for oilfield services. First of all, we are interested in maintaining the loyalty of experienced personnel and personnel development, but we strive to become a center of attraction for young industry specialists in order to improve their professional competencies.
By: Ivanova, A.
Source: Neftegaz.ru